Customer Background
Our client is a leading supplier of construction materials, offering products like lumber, drywall, and roofing. Serving both contractors and DIY enthusiasts, they are known for quality, expert advice, and reliable service. Their extensive inventory supports diverse projects, from residential to commercial. Strong supplier relationships and commitment to customer satisfaction underpin their reputation for excellence.
-
Industry
Manufacturing
-
Technologies / Platforms / Frameworks
Power Platform: Power Apps, Power Automate
MS SQL server: Azure & Cloud
File storage: LCR Blob Storage
Challenges
The company faced challenges in managing its extensive fleet operations and ensuring efficient logistics. They were also working to better coordinate large-scale projects across multiple locations. The challenges include:
Vehicle maintenance issues
Struggle with unplanned vehicle breakdowns, maintenance delays leading to service interruptions, time-consuming, and increase repair costs.
Fleet tracking
The lack of real-time tracking made it difficult to monitor vehicle locations, resulting in inefficient route planning and delayed deliveries.
Management complexity
Coordinating fleet maintenance schedules and tracking vehicle performance was cumbersome and prone to errors.
Solutions
After having an in-depth discussion with the client, we suggested using Power Apps to address their complex challenge. This customized app streamlined the tracking process and integrated the features that improve the coordination among them. It includes:
Master plan log
The master plan log was introduced to improve overall ongoing projects and provides the following key benefits:
- Centralized project management: All construction projects were logged into a single system, allowing management to monitor progress, assign resources, and track deadlines in real-time.
- Improved collaboration: The app enabled cross-department collaboration by allowing them to access and update project information from anywhere, reducing miscommunication and task duplication.
- Resource optimization: A clear view of project timelines and resource needs allow them to allocate manpower, equipment, and materials more effectively, reducing waste and delays.
Fleet tracking manager
The implementation of the fleet tracking manager system transformed their fleet of vehicles, offering the following improvements:
- Real-time tracking: The system offers live GPS tracking, giving the logistics team real-time visibility into each truck’s location and status, enabling quick adjustments to routes and schedules.
- Route optimization: The fleet tracking manager’s route optimization feature enables the company to minimize fuel consumption and reduced delivery times by identifying the most efficient routes.
- Preventative maintenance: The app helps managers to monitor vehicle usage and scheduled maintenance, preventing unexpected breakdowns and minimizing downtime.
Benefits
Improve efficiency
Real-time tracking and optimized routing reduced delivery times and fuel consumption, leading to cost savings and enhanced customer satisfaction.
Minimize downtime
Automate maintenance scheduling, minimize unexpected breakdowns to ensure vehicles were consistently operational and reducing repair costs.
Enhanced management
The centralized system streamlined fleet management, providing better oversight and data-driven decision making, ultimately improving overall operational efficiency.
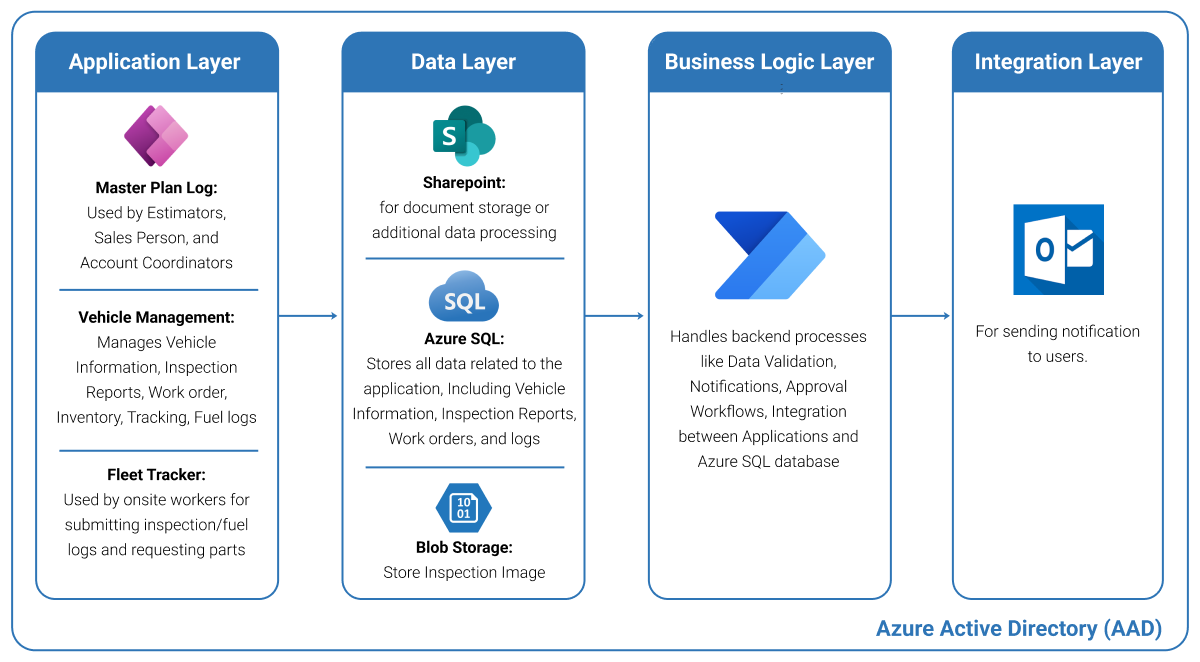
Need more information?
Tell us what you are looking for and we will get back to you right away!