Customer Background
Our client is a specialized aerospace manufacturer with over 20 years of experience, delivering critical components for both commercial and defense aviation sectors. They operate multiple production facilities and are committed to precision and innovation. As they expanded, they sought to enhance manufacturing quality and ensure compliance with stringent safety standards to maintain their trusted partnership in the industry.
-
Industry
Manufacturing
-
Technologies / Platforms / Frameworks
Azure Machine Learning Studio, TensorFlow, Keras, OpenCV, scikit-learn, NumPy, Python Imaging Library
Challenges
- Quality control issues: The recent audits of their manufacturing unit revealed that there was an alarming increase in production defects. While this raised concerns about product reliability, the looming threat was the potential diminishing impact on customer relations.
- Regulatory compliance: There was significant pressure to realign with the safety and quality standards. While continued failure in meeting protocol standards would’ve meant incurring hefty fines, the company’s greatest concern was irreversible damage to the brand’s reputation.
- Inefficient monitoring: Putting more hours of manual inspection meant consuming time that was not there to be spared and being more prone to human error. Extended use of a system laid with inefficiencies resulted in increased operations costs and further jeopardizing the quality control efforts.
- Risk of component failures: When enough defects go unchecked, they pose a great risk of leading to a catastrophic failure. The industry in question cannot afford such an event since it directly endangers passenger safety, causes legal exposure, while damaging the company’s reputation.
- Data integration issues: The client struggled with integrating data from various manufacturing systems and processes. Inconsistent data formats and silos hindered real-time visibility into production metrics, complicating the identification of quality issues and making it difficult to implement timely interventions.
Solutions
During our consultation, we thoroughly assessed the client’s challenges and engaged in collaborative thought exchange sessions. Through constructive discussions with the client, we identified key opportunities to leverage AI and advanced analytics to modernize the client’s manufacturing processes. Ultimately we formulated a tailored solution that effectively addressed their needs ensuring seamless improvements in quality control and operational efficiency, that helped them align with safety standards.
- Real-time monitoring: We deployed an AI-driven video analytics system to continuously monitor production lines, capturing high-resolution footage for immediate defect detection. The system allowed the client not only to proactively identify the issues in real time, but also enabled to take swift corrective measures that minimized risks pertaining to defective products being passed due to oversight during the manufacturing process.
- Automated alerts: The solution we delivered is integrated with an automated alert system that alerts the quality control team through a notification anytime a defect is detected in the production line. The functionality ensures flagging of issues assigned high priorities. Promptly dealing with such issues significantly reduces the error rates and gives a boost to the overall product quality. Hence, a culture of continuous improvement is inculcated in manufacturing practices.
- Predictive maintenance: Our advanced analytics system also monitors equipment performance. Forecast models are run using machine learning that predict potential failures. IoT-based sensors are used to continuously capture real-time data from machinery, such as temperature, vibration, and pressure levels. The data is analyzed alongside historical patterns to enhance accuracy in failure predictions. By leveraging machine learning algorithms, the system identifies potential issues and recommends preventive measures before a failure occurs. The predictive maintenance system supports the client in scheduling timely maintenance. Periodic checks help in minimizing downtime and maintain operational efficiency throughout the manufacturing cycle.
- Seamless integration: We carefully designed the solution to ensure it integrates seamlessly with the client’s existing systems. This compatibility allowed for immediate enhancements to their quality control processes, empowering the client to optimize operations without the need for a complete overhaul of their established workflows.
Benefits
- Improved defect detection: Enhanced accuracy in identifying defects, reducing reliance on manual inspections.
- Enhanced operational efficiency: Predictive maintenance reduced downtime and increased overall production efficiency.
- Regulatory compliance: Automated monitoring ensured consistent adherence to safety and quality standards.
- Optimized data integration: Seamless integration provided real-time production data access for better decision-making.
- 75%
Reduction in time to
access production data - 60%
Increase in defect
detection speed - 80%
Improvement in resource
utilization scalability - 30%
Decrease in operational
downtime
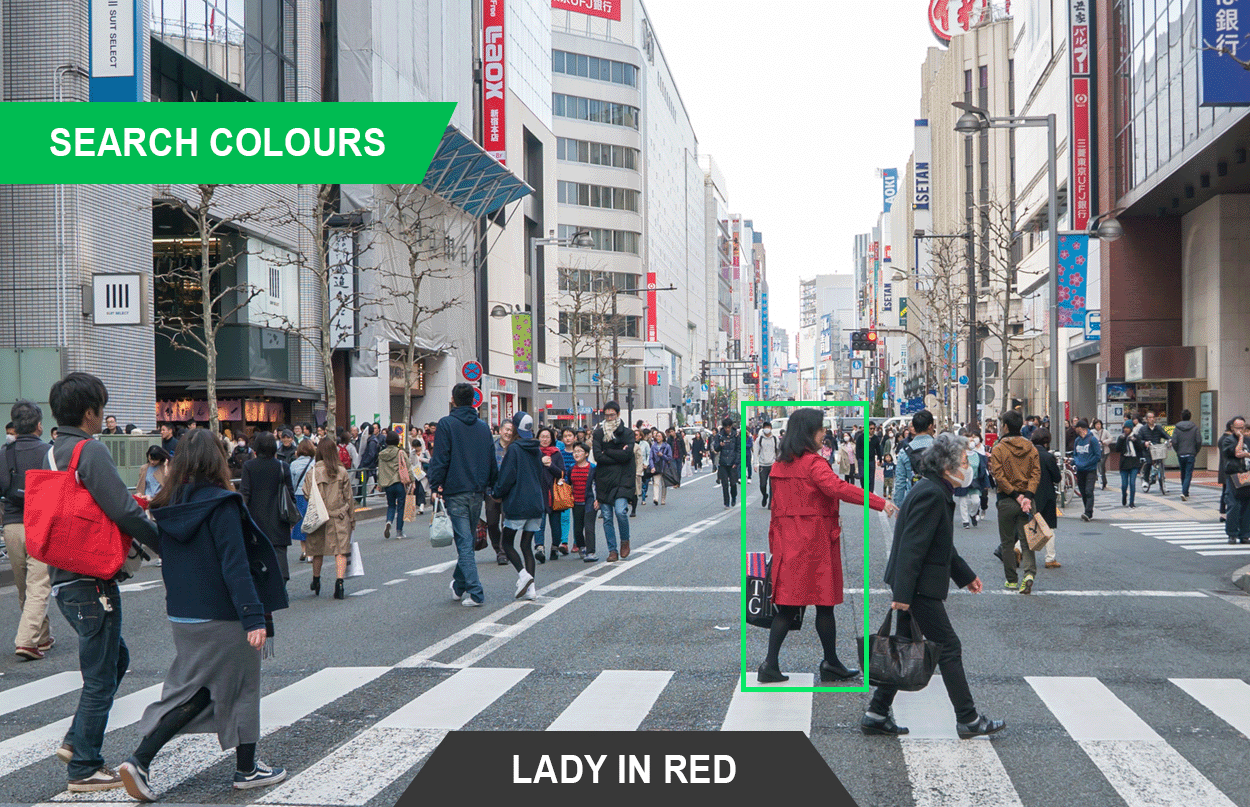
Need more information?
Tell us what you are looking for and we will get back to you right away!