The Internet of Things (IoT) is connecting everyday objects and equipment to the internet using microchips and sensors. This is enabling non-living items to exchange data and communicate with each other. Almost every industry is incorporating IoT and leveraging its benefits now. And when it comes to manufacturing and packaging industries, IoT is expected to transform them completely by empowering manufacturers to track and measure every element of their operations.
IoT is enhancing equipment operational efficiency in these industries by interconnecting machines, people and processes. A smart packaging system provides insights that you can use to modify packaging processes for better performance.
Challenges faced by the packaging industry
Just like every other industry, the packaging industry also uses a lot of mechanical equipment like packing scales, process weighing systems among others. These equipment are susceptible to damage and failures due to various reasons. Malfunction of equipment leads to downtime, which results in a loss for manufacturers, while inaccuracy of a weighing scale leads to either over-weighing or under-weighing of the material, in turn resulting in loss for the company. In the first case, it would be a financial loss, whereas it would lead to regulatory fines or loss in production time in the second case. Hence weighing scales and other equipment must be maintained to function properly.
Here are some of the ways how IoT can help packaging industries
Automation of legacy systems
Till sometime back, it was quite complicated to connect manufacturing equipment to the Internet of Things. This is because older, legacy equipment comprised of manually operated machinery, outdated PLCs to control manufacturing process, stand-alone computer numerical control (CNCs) that control machine tools such as lathes and grinders and older automation systems.
The thought of interconnecting machines and connecting them to the internet was a fairytale until IoT was introduced. Also, these traditional systems were not designed to function with modern IoT technologies. Hence it required expensive upgrades and custom development to bring a manufacturing plant into the IoT age.
This has completely changed due to a drop in the costs, the availability of flexible new technologies and companies specializing in IoT and embedded technologies. Due to these factors, it has become easier and more affordable to integrate IoT in legacy equipment.
According to Goldman Sachs and BI Intelligence Estimates, the cost of IoT sensors has been gradually decreasing since 2004. The average cost of IoT sensors dropped by more than half, from $1.30 to $0.60 between 2004 and 2014. These prices are expected to lower more by 37% to $0.38 by 2020.
With such slashes in prices of IoT sensors, most companies are now able to take advantage of this technological transformation unlike before.
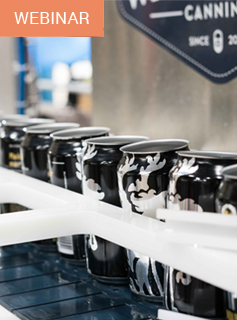
How Industry 4.0 is a game changer for factory owners
Webinar agenda
- How Industry 4.0 is a game changer
- The role of IoT and data analytics in the manufacturing industry
- IT/OT Convergence: Why it’s important for IoT adoption
- Current market trends and value
- Smart factory: The evolution not revolution
- Demo and review of smart production line monitoring
- Q&A session
Real-time insights help in anomaly detection
The incorporation of IoT devices on your packaging factory floor and throughout the inventory gives you real-time actionable insights through data analytics. These insights help you to take proactive actions and address any arising issue with the asset in real-time to continue hassle-free production. You can also analyze the insights and make important decisions for your factory management, business enhancement and increasing your workforce efficiency.
This requires an IoT asset management platform to support various devices, communication protocols, networks and cloud environments. This platform is supposed to be integrated with current enterprise systems.
Predictive maintenance
Failure of equipment adversely affects inventory, goods outcome, delivery and leads to downtime. Hence, companies spend a huge amount on the maintenance of equipment. There are many sensor-based applications and devices that help companies to predict and prevent the maintenance needs of the factory floor. Thus, they help you save a decent amount on maintenance costs and prevent the loss that occurs due to equipment downtime.
According to Markets and Markets Research, the smart factory market is projected to reach 205.42 Billion USD by 2022, growing at a CAGR of 9.3% between 2017 and 2022.
The IoT service providers analyze your internal information technology systems as well as operational technology landscape and ascertain your goals, key performance indicators, system capacity, minimum performance parameters, interface requirements, data capture points and other required features. They document the complete definition, architecture, design and plan of the IoT platform, solution or product that fits your needs and deliver custom sensors, gateway and hardware design with the right set of required protocols (BLE, ZigBee, Wi-Fi etc.).
The final say
Use of IoT in packaging is relatively new. But as expected, IoT solutions for the packaging industry help to do everything that is required in packaging. IoT helps to cut on packaging costs and improve logistics management, inventory optimization, customer experience, branding and brand protection.
IoT also helps in improving the quality of a finished product, reducing waste, increasing line speed and optimizing bottom-line costs. Smart factory enables you to track and trace product deterioration on the factory floor. IoT is already transforming the packaging industry and this will become more prominent in the coming years. Contact us for a free demo and know more about smart factory for packaging.