Chemical producers want to address compressed air leaks that jeopardize their production processes. A leak in the nitrogen blanketing system is unsafe to the employees, equipment and product quality. The US EPA estimates each year 240,000 water pipeline leaks result in 2.1 trillion tons of water loss. That’s enough to supply 60 million Americans every year.
For energy, utilities as well as oil and gas companies – healthy pipeline networks are critical. Pipeline leaks can cause asset loss, production loss, life loss and environmental damage. Among these different aspects, survey companies measured downtime.
The world’s largest manufacturers lose almost $1 trillion a year, or $532,000 per hour, to downtime. – The True Cost of Downtime report by Senseye.
Companies always plan and construct a pipeline network that withstands rigorous conditions. However, wear, corrosion or pipeline infrastructure damage make liquid or gas leaks an unavoidable problem. Automatic leak detection helps enterprises and governments:
A need for automatic leak detection
Pipeline leaks were traditionally monitored through manual inspection by an expert. The competency of the inspector and the frequency of assessments are limitations of human checks. In chemical plants, not every condition is suitable for human exposure. Oil and gas leaks can cause pollution, fatal accidents, assets loss and hefty fines from regulatory agencies.
An automatic leak detection system is less labor-intensive and highly accurate. It also saves companies time, cost and lives. Remote operation requires appropriate remote data acquisition. Following it, suitable data analysis methods help accomplish remote monitoring.
Challenges with traditional leak detection methods
Every pipeline and the product batch it carries have their own characteristics. This affects leak detection monitoring system’s efficiency.
For example, gas pipelines with large diameter poses situations of increases and decreases in pressure and flow. It may not reflect in distant parts of the pipeline for hours. Direct observation techniques and other sophisticated techniques like odorization as well as acoustic methods have limitations in capturing such fine movements.
Traditional leak detection methods for crude pipelines face challenges in detecting the flow rate and pressure waves’ speed. While SCADA-based computational methods or flow balancing can generate false leak alarms.
Other traditional leak detection methods like direct burial detection systems, negative pressure wave detection system and pig-based monitoring also have some or the other challenges.
What if you can:
- Detect leaks as small as <1% of total flow in real-time?
- Rely on leak detection monitoring system with zero false alarms?
- Distill pipeline monitoring data into useful, easy-to-read charts and dashboards?
Traditional methods of detecting pipeline leakage and localization cannot fulfill the above benefits. That motivates the enterprises and governments to use vision-based leak detection monitoring system. Softweb Solutions’ AI-powered leak detection monitoring system does automatic leak detection using computer vision through the following workflow.
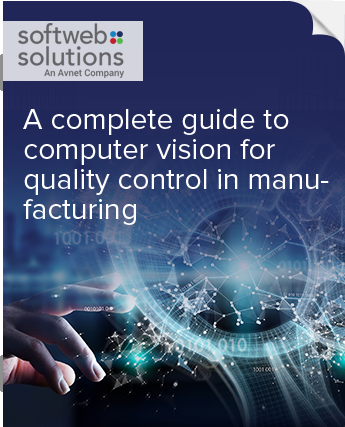
A complete guide to computer vision for quality control in manufacturing
Whether you want to learn how to design a computer vision system for quality control (just by following six steps) or know how to use computer vision solutions for quality control in manufacturing, your answers are just a download away from this whitepaper.
Workflow of Softweb Solutions’ leak detection system using computer vision
- Smart cameras installed in remote locations and connected to IoTConnect
- Constant data acquisition
- Pre-processing and sampling
- Feature vector calculation
- Training bidirectional CNNs
- Real-time leak detection
Softweb Solutions’ AI-powered leak detection monitoring system utilizes KPIs of the pipeline and the product batch it carries. Our system uses different statistical approaches. The sequential probability ratio test is one of the widely used. It characterizes and distinguishes the ‘normal’ and ‘abnormal’ behavior of the pipeline and the product it carries. The system improves accuracy using historical and live data as the software tracks different KPIs.
Our automated leak detection software is not limited to pipeline leak detection. It can also identify anomalies like flow meter errors, compressor issues, inlet separator water level problems, etc.
What opportunities can you grab with a leak detection system using computer vision?
First, one can easily customize the system as per their operations’ requirements. Permitted users can instantly update data from anywhere, anytime, using the mobile app. It also compliments with existing SCADA system.
Remote data access and analytics are a boon for pipeline network maintenance. An intelligent alarming feature of the system nullifies trips to field sites. The customized reporting feature provides precise analytics for regulatory and environmental agencies. A single dashboard displays the operational status of the pipeline, flow and pressure rates, and other defined KPIs.
Why to adopt a data-driven approach for leak detection monitoring and localization
Usually, solutions providers categorize leak detection monitoring techniques into three groups. The first group of methods includes a process model and physical model for leak detection.
Here, the methods consider physical properties of liquid like:
- Density
- Pressure
- Temperature
- Velocity
Leakage detection occurs when the physical properties of the liquid in the pipelines deviate from the defined physical properties.
The second group of methods jointly uses physical models and sensor data. Sensors’ data is combined with a physical process model. And then, the sensors’ measured data are classified after comparison with the derived model. Here, the data-driven methods perform the classification step.
The last group derives a process model by combining sensor data like pressure and flow with data analysis methods. The derived model classifies the conditions of the pipelines’ physical properties. It even identifies the leaks as small as <1% of total flow. Undoubtedly, data-driven approaches require a solid understanding of the pipeline and material characteristics. That’s why data-driven strategies are faster, more accurate and reliable.
Leak detection monitoring system at its best
Computer vision techniques usually gather images or video data through infrared cameras or sensors. Under data-driven approaches, solution providers apply segmentation, object detection, convolutional neural network, etc., on images or video data for leakage detection and localization.
The performance of leak detection monitoring system varies from one pipeline to another. It depends on variables like diameter, communication, instrumentation, leak detection method, topology and modes of operation. Given the enormous volume of product transported in pipelines, by no means can any company bear even a small leak for a short time.
Considering that, a leak detection system’s sensitivity and detection time are critical factors. Hence, look no further than the leak detection system using computer vision as it detects pipeline leaks when it occurs.