The biggest change that the manufacturing industry is experiencing right now is the Internet of Things (IoT). The first industrial revolution was largely powered by steam power and today IoT-centric solutions are powering the fourth industrial revolution.
Sensors are central to IoT solutions in factories; gathering data from machines and delivering them to the right people at the right time. A survey by PwC showed that at least one-third of the manufacturers in the U.S. are embedding sensors in their factories and using the data generated to make their operations more efficient. 34% of manufacturers believe it is critical for American companies to adopt an IoT strategy and 38% say that they are using embedded sensors in products that allow their end-users and customers to collect sensor-generated data.
Factories are placing sensors and controllers on the assembly line which report the components’ status in real-time. Manufacturers now have the ability to connect machine-to-machine cells, conveyor lines, RFID and Wi-Fi Safety systems, and energy subsystems with ERP and supply chain systems including warehouse management systems, across a single-standard IP networking platform. In this way, smart manufacturing is leading the way towards a new industrial revolution. A smart manufacturing solution implemented in the factory displays five key factors towards a more advanced industrial revolution:
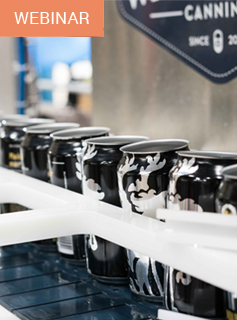
How Industry 4.0 is a game changer for factory owners
Webinar agenda
- How Industry 4.0 is a game changer
- The role of IoT and data analytics in the manufacturing industry
- IT/OT Convergence: Why it’s important for IoT adoption
- Current market trends and value
- Smart factory: The evolution not revolution
- Demo and review of smart production line monitoring
- Q&A session
1. Increased Factory Visibility
Floor managers get to view production line data from any location on their smartphones and tablets. If there is a quality control problem, the supervisor can quickly shut down the process before defective products are manufactured. In more advanced IoT solutions, machines will be automatically shut down if a process deviates from the parameters that have been set. The repair and operations industry is set to undergo a huge change because of the ability to track the wear and tear of machines 24/7/365. Manufacturers will be able to lease capital intensive equipment on a per-hour basis instead of purchasing it.
2. The Supply Chain Becomes Smarter
Smart manufacturing also includes making the supply chain more intelligent. Sensors and RFID tags can be placed on the products so that as they move across the supply chain, the tag readers placed throughout the system will keep recording their location and condition. IoT solutions can enable manufacturers to track their inventory and get remote inventory level monitoring ability.
3. Energy and Utility Costs Get Cut Down
Energy usage accounts for one of the biggest expenses for factories. Smart factories can also help businesses cut down on energy consumption. By setting up a network of smart grids, smart meters and sensors throughout the factory, the devices can communicate to each other to ensure load balancing and reduce unnecessary energy consumption during high peak periods. This is done by smart networks which communicate with devices to access how much energy is being used and when. IoT-enabled HVAC systems also offer businesses weather data reports and prediction analysis to help them plan their energy usage.
4. Fewer Human Resources Needed
A manufacturing company that has implemented IoT solutions will be able to cut down on its field service expenses since it is getting continuous data regarding the condition of its installed equipment. In our use case, we can assume that for company Smart Makers Inc., each field service technician deployed in the field has a capacity of ten on-site customer visits per week.
The expected results for implementing remote service would be a reduction in total on-site visits by 30%. The rate for a field service technician is $100 per hour.
STEP 1:
Determine the number of visits per week, assuming that an average field-service visit at a customer location is four hours long. 40 hours per week/4 hours per visit = 10 ten calls on average per field service technician per week.
STEP 2:
Determine the man-hours saved by using IoT to remotely diagnose and repair 30% fewer issues
without an on-site visit. 10 calls x 30% x 4 hours = 12 man-hours saved per week.
STEP 3:
Develop a quantifiable metric; subtract the amount of time required per work week times the rate for a field service technician to determine labor cost savings. 12 hours per week x $100 per hour = $1,200 in savings per work week.
STEP 4:
Determine the impact across the entire field service organization. Assuming 100 technicians x 50 work weeks x $1,200 per work week = $6,000,000 in annual savings.
5. Increased Product Revenue
Continuing with our previous example, Smart Makers Inc., can also increase its product revenue with IoT solutions. The company estimates that a connected product line could generate an additional revenue stream based on IoT-enabled value-added services.
Assuming customers will subscribe to these services within the first year of product ownership, here is a sample calculation of increased revenue:
STEP 1:
Determine the value of connected product services for each product unit assuming the average selling price of a connected application is $50 per year, per user, and the average number of users per connected product is 20. $50 x 20 users per product = $1,000 per product
STEP 2:
Estimate the total product revenue increase. Assuming a 25% attach rate on a total product unit volume of 100,000, the increase in product revenue for the new connected application would be 100,000 units x 25% x $1,000 = $25,000,000 increase in annual revenue.
The Internet of Things is also a cost effective solution for most manufacturers. Open source platforms, low-cost sensors, cheap microchips and accelerometers are bringing down the hardware costs. The Big Data that is generated from implementing IoT can be hosted cheaply on the cloud using platforms such as Azure IoT services. The Machine Learning tools offered by the service helps companies in carrying out predictive analysis and the Power BI tool gives employees the ability to view the data on user-friendly Excel spreadsheets.
Source: tech.co