Introduction
We are in the midst of a global level revolution – Industry 4.0, where every business is implementing the Internet of Things in one or the other form in order to have better outcomes. Even factories today are adopting the latest trends of the Internet of Things. As a result, these factories are transforming themselves into a “smart factory”. But, how are they evolving? What makes them a future-ready factory?
The answer is an IoT-enabled smart factory or production line monitoring solution. A production line monitoring (smart factory) solution is designed and developed to gather data from the equipment and machinery present on the shop floor and help a floor supervisor to monitor, analyze, and manage the machinery.
To keep up with the latest trends of IoT and business requirements of the clients, Softweb Solutions has developed an indigenous production line monitoring solution – Softweb Smart Factory. Be it ongoing job stats, reports or monitoring the data generated by the equipment and machinery in a factory, Softweb Smart Factory can explicitly perform these tasks for supervisors and stakeholders.
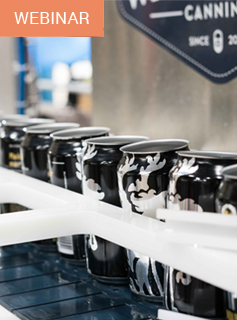
How Industry 4.0 is a game changer for factory owners
Webinar agenda
- How Industry 4.0 is a game changer
- The role of IoT and data analytics in the manufacturing industry
- IT/OT Convergence: Why it’s important for IoT adoption
- Current market trends and value
- Smart factory: The evolution not revolution
- Demo and review of smart production line monitoring
- Q&A session
When and where to implement Softweb Smart Factory solution
Softweb Smart Factory is developed to aid manufacturing firms in improving their business processes and reduce the downtime as a result of equipment failure or any other untoward incidents on the shop floor.
So what are the situations where Softweb Smart Factory can really come in handy? Below are some such scenarios where Softweb’s production line monitoring solution can play a crucial role;
Scenario 1: Unbalanced workload at the station
Bottlenecks and issues related to efficiencies may occur in a production line where a station is under or over utilized. The toggle between balanced and unbalanced station utilization can lead to manual intervention in task assigning and setting the timing standards, which may reflect as excess time consumption at a particular station resulting in a delay in delivering the final product.
Solution
Softweb Smart Factory solution offers the advantage of monitoring the average time required to accomplish a job on the production line. As a result, supervisors can have more precise time estimates to appropriately balance the production line.
Scenario 2: Lack of real-time information
There may be a situation where some businesses lack proper infrastructure or tools that can monitor production lines from a central location. This may result in a delay in transferring the information to the respective authorities.
Solution
Softweb Smart Factory solution represents a context-sensitive factory environment that can track and monitor the turbulent activities on the shop floor in real-time using decentralized information and communication structure for optimum management of production processes.
Scenario 3: Sudden breakdowns of the production line
A product can be delivered to the customer in the committed duration of time, if, and only if, every machine associated in the factory works properly and precisely. However, there may be some situations when there is sudden breakdown in the production line itself which increases the downtime in the factory.
Solution
Softweb’s production line monitoring solution facilitates factories with predictive maintenance, which helps companies to predict a breakdown long before it occurs. The solution tallies the historical pattern and compares it with the current working pattern of the production line. Moreover, the production line monitoring solution detects any anomalies that may affect the working of the production line.
Scenario 4: Production cycle
Unnecessary buffers like products not meeting the quality expected by customers, delay in production because of machine breakdown or raw material is not up to the mark, may arise as a result of lack of proper information and data or any unrealistic insights into a production line. Such buffers may negatively affect a business’s bottom line.
Solution
The production line monitoring solution by Softweb Solutions allows a business to monitor the cycle time, production lead time, and product related tasks. This, as a result, equips stakeholders with real-time data which further facilitates them with the information of the station where unnecessary tasks are being carried out. The overall process gives supervisors the access to data which can help them to improve their production cycle times.
Scenario 5: Production quality
For a business to be in the game and generate more profit, quality matters big time. However, there may arise a situation when any equipment in the production line may not be able to deliver the quality it was supposed to deliver. With the absence of a proper platform, identifying stations or locations where the quality issues are being generated may become quite chaotic.
Solution
Softweb Smart Factory solution provides a diverse spectrum of information from machine to machine in a production line. This allows users to monitor machinery present on the production line thoroughly from a remote location. With the help of insights delivered by the solution, a factory can maintain the quality standards.
So, these were the “WHENs” and “WHEREs” for implementing Softweb Smart Factory solution. However, why to implement the solution in your factory is another question to be answered.
To make it easier, let’s have a look the benefits of implementing Softweb’s production line monitoring solution in a factory.
Benefits
Real-time visibility
Softweb Smart Factory allows businesses to monitor the machine performance in real-time and take better decisions in order to avoid downtime and production loss.
Prescriptive analytics
The solution allows organizations to maximize the outcomes on the basis of decisions based on predictive analytics and ensure sustained performance in addition to consistent performance.
Integrated supply chain management
Softweb’s production line monitoring solution revolutionizes the perspective of designing, production, and delivery of products while elevating the efficiencies and overall performance of the factory with the connected supply chain.
Productivity improvements
With the capability of adapting abrupt fluctuations in production levels and uninterrupted supply of insightful data, Softweb’s production line monitoring solution assists business heads to keep on improving their business processes for better productivity.
This brings us to the end of this article; however, before summing up, we would like to show how Softweb Smart Factory solution can be implemented in a factory;
Step 1: Site assessment
Our team visits the client site to assess and analyze the infrastructure, production capabilities, and the performance of production lines.
Step 2: Data point analysis and hardware kit finalization
Post site assessment, based on the results, the team suggests the hardware and sensors that can be installed in the factory. In this step, the team also conceptualizes the flow of the data and where it shall be stored.
Step 3: Data acquisition and analysis
Once the hardware has been installed and the flow has been conceptualized, the data generated from the sensors and other devices is collected and analyzed.
Step 4: Data visualization
With help of the latest visualizing tools, the data generated is processed and presented as actionable insights in the form of visuals. The visuals help supervisors to understand the overall functionality of the production line which in turn helps them to have better decision making capabilities.
Conclusion
Our production line monitoring solution is designed to offer a single window monitoring solution to businesses. The solution offers a blend of actionable insights, visuals and information to improve the productivity of a factory.