The world is changing dramatically today. The desire to take business to a new level drives the will of entrepreneurs. To get a better result and generate more profit, businessmen are investing tremendously in technologies to enhance the manufacturing processes. They are having state of the art machinery that can accomplish a task in few hours, which initially would take a couple of days to finish. However, the essential data that make these machineries work efficiently has to be taken down manually on paper.
Because of these manual processes, the job on the production line may deviate from the accuracy it was supposed to maintain. In this technology driven world, why not use the benefits and advantages the latest technologies provide. One such solution that can drive better results from your production lines is an IoT-enabled smart factory solution.
To give you a brief idea about the benefits you can get from a smart factory or a production line monitoring solution, allow us to show how you can get over certain challenges you might be facing in your factory.
Challenge 1 – Lack of real-time information
There are many industries that lack a proper infrastructure or tools to monitor the complete production line from a central location. This results in a delay in transferring the information to the respective authorities.
Solution
Whether one needs currently running job information, periodic report updates or data to monitor operation of the production line, having a system that can exclusively perform all these tasks is always a plus for the factory. Smart factory offers the supervisor real-time, continuous and standardized task level data to provide the detailed analysis performance of the factory. With a better knowledge of their production lines, supervisors can easily make out the problematic areas and make accurate decisions to meet the dynamic demands of their production lines.
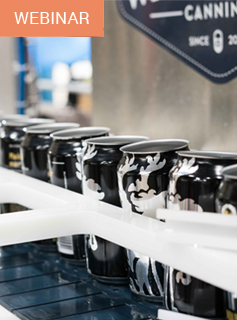
How Industry 4.0 is a game changer for factory owners
Webinar agenda
- How Industry 4.0 is a game changer
- The role of IoT and data analytics in the manufacturing industry
- IT/OT Convergence: Why it’s important for IoT adoption
- Current market trends and value
- Smart factory: The evolution not revolution
- Demo and review of smart production line monitoring
- Q&A session
Challenge 2 – Unbalanced workload at the stations
In case any of your station is underutilized or over utilized, there are possibilities that you may encounter bottlenecks and efficiency issues. The toggle of production line between balanced and unbalanced utilization can be the result of manual intervention in task assigning and setting the timing standards. These standards and interventions may or may not reflect the precise time consumption at a particular station causing a delay in development of the final product.
Solution
The quality control, data collection and statistical analysis functionalities of a smart factory solution are compatible with almost any type of station in a production line. This solution offers the advantage of monitoring the average time required to accomplish any interconnected jobs. This in turn allows supervisors to have more precise time estimates to appropriately balance the production line.
Challenge 3 – Extended changeover time
There might be instances when you might be thinking that you need a solution for a quicker production line changeover. However, you might be skipping this idea because of the cost and time involved in conducting a changeover process. It is needless to say that the process will affect the production in your factory.
Solution
A smart factory solution offers rich insights that can be used to monitor the production line phase by phase. In case of a changeover, the smart factory solution can help in identifying the station that is to be changed or replaced. This precise information helps you to cut the lengthy change over time in half.
Challenge 4 – Production cycle time
The lack of proper information and data of your production line or unrealistic insights may lead to unnecessary buffers. These buffers may negatively affect a business’ bottom line.
Solution
A smart factory solution allows you to monitor the cycle time; non-confronting product related tasks and production lead time. This allows you to have real-time data which in turn allows you to make out the station where unnecessary production is occurring. The overall process offers the supervisor access to the data which may help them reduce or eliminate the issue causing the loss of asset and time.
Challenge 5 – Production quality
In order to be in the business and generate more profit, the quality of the final product matters big time. However, with the absence of a proper platform, identifying stations or locations where the quality issues are being generated may become quite chaotic. Once the faulty station is identified, figuring out the reason for the quality difference is a different ball game altogether.
Solution
A smart factory solution provides a diverse spectrum of information from station to station in a production line. This allows users to monitor every station thoroughly from a remote location. With the help of insights delivered by a smart factory solution, a factory can maintain the quality standards.
If you are looking to implement a smart factory solution in your factory, Get in touch with us.